Reports: ND952539-ND9: Fundamental Studies of the Removal of Particulate Fines From Solvents Using Water Droplets as Collector Particles
Arun Ramchandran, University of Toronto
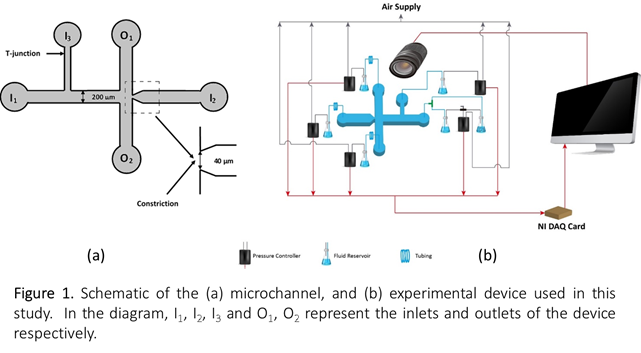
Introduction
The objective of this project was to assess the potential of water-based “froth flotation”, i.e. the removal fine hydrophilic particulate matter suspended in an organic medium by adding water droplets to the medium that serve as collectors for the particles. The application is in a new process initiative in the oil sands area called non-aqueous extraction, whereby an organic solvent, instead of water, is used to dissolve the bitumen coating the surface of the oil sands particles. A key challenge in this alternative process is the removal of the fine (<10 μm), hydrophilic clay particles in the solvent. The instrument developed in this project permits quantitative assessment of the water-based froth flotation idea to solve this challenge.
To allow capture of particles by water droplets in the organic medium, collision events need to be established between the water droplets and particles via a mixing device. The critical question, therefore, is, what is the efficiency of a hydrodynamically-induced drop-particle collision to lead to capture? Given the materials, this efficiency depends on the water drop size, the particle size relative to drop size and the flow conditions. Our instrument allows us to execute controlled collisions between particles and a single drop, and measure the effect of the above variables on the capture efficiency of a collision.
Experimental Details
The drop-particle impingement experiments were conducted in a five-port device with a constriction at the mouth of one of its arms and with a liquid reservoir connected to each port. The flow rate through the inlets (I1, I2 and I3) and the outlets (O1, O2) creates a pressure differential and, in turn, the drop can be held stationary at the constriction at different flow rate combinations by altering the pressures maintained in the reservoirs. The channel dimensions are shown in Fig. 1(a). Light mineral oil was used as the continuous phase. Glycerol/water (70 v % glycerol) mixture was used as the dispersed phase. Hollow glass beads of density 1.01 g/cc and 10.0 µm mean diameter were used as the particles in this study.
Procedure
The water-in-oil droplet was generated at the T-junction between the channels leading out of I1 (oil reservoir) and I3 (water reservoir), and the size of the water/glycerol slug was controlled by regulating the ratio of the flow rates of water and oil [Fig. 1(a)]. The required water drop was held firmly at the constriction by suction (Fig. 2). Mineral oil containing the glass beads was introduced from inlet I1, and approached the drop. The particles either bypassed the drop, or were captured by the drop (by adsorption, but in most cases, by penetration). These events were recorded using a camera controlled by a computer [see Fig. 1(b)]. The video images were analyzed in MATLAB®, and a particle tracking algorithm was used to record the fate of each particle.
Results
An example of the distribution of collision efficiency over the device width is shown in Fig. 3. Owing to the low velocities near the stagnation point, particles have longer interaction time with the drop surface, ensuring higher capture efficiency when compared to those travelling away from the centerline.
Figure 4 shows that the fraction of particles that are captured by the drop, as a function of the applied strain rate, displays a maximum. At present, we do not have concrete explanation for this. However, we are confident that hydrodynamic drainage is not the governing/rate limiting process for our study. From scaling estimates, it was seen that the film drainage time for our system is
seconds, which is much shorter than particle-drop capture times.
The fraction of particles captured by the drop is determined for varied drop diameters. The particle capture efficiency is plotted against the drop diameter for a fixed flow rate of 1.82 µl/min in Fig.5 (a). From the trend it is evident that a drop with a larger diameter, captures more particles as opposed to smaller diameter drops for a fixed flow rate. This is because a larger drop occupies a larger cross-sectional area, encompassing more streamlines thus ensuring more particle capture.
Experimental results showed that for a drop size of 100 µm and flow rate of 0.862 µl/min, for a viscosity ratio less than 1, the capture efficiency is very low at about 0.249. A viscosity ratio of 1 yields a higher efficiency of 0.804. Further increase in the viscosity ratio to 3.28, again lowers the capture efficiency. The trend is shown in Figure 5(b).
We have thus demonstrated a possible inexpensive and efficient strategy for particulate capture using water drops without the addition of external chemicals or surfactants. An optimal combination of the drop size, flow conditions and viscosity ratio will result in maximizing the efficiency of particulate removal.
Simulations
Parallel to the experiments, we have been performing boundary simulations of the penetration of a particle into a drop under constant force conditions (see Fig. 6 for schematic), with the objective of determining the quantity of water that is entrained during this process. Note that in the non-aqueous oil sands extraction, the particles engulfed by the drops will also bring some solvent, and hence bitumen, into the water drops (see Fig. 7). Our calculations indicate that even for very artificially high Hamaker constants, the water entrained by the particles is less than the particle volume, showing that this effect can be ignored (Fig. 8). These simulations could, however, be used to get the flow conditions required to produce a nanometer thick coatings on micrometer sized particles.
To establish expertise in simulations involving moving contact lines, we considered the problem of a Janus drop placed in a uniaxial extensional flow. We have established a boundary integral equation that involves the prescription of only the velocities and curvatures at the various interfaces, eliminating calculation of singular stresses at the contact line.
Three manuscripts will ultimately result from this work. The development of the instrument has also allowed us to secure industrial funding from Syncrude Canada, which is a major oil sands company in Canada.