Back to Table of Contents
45642-AC4
Improving Terephthalic Acid Synthesis in High-Temperature Water
Phillip E. Savage, University of Michigan
Introduction
Terephthalic acid is a commodity
chemical, and its main use is in the production of polyethylene terephthalate,
a polymer used to make synthetic fibers and beverage containers. Terephthalic acid is produced commercially
in acetic acid, and then purified by hydrogenation in high-temperature
water. If water were used as the
medium for the synthesis step, a simpler process may be possible because there
would be no need to change solvents for the two steps. Moreover, water is a byproduct from the
oxidation so the current process includes a tall distillation column for
separating acetic acid, so it can be recycled, and water. If water were the reaction medium for
terephthalic acid synthesis, the need for this column and its operating costs
would be eliminated. The cost of
this tower is significant both because of its size and its internals requiring
titanium to withstand the corrosive conditions. Finally, the bromide catalysts used react with acetic acid
to form small amounts of methyl bromide. This pollutant must be removed from the gaseous effluent
stream. If water were the solvent,
no methyl bromide would form so the process would be less polluting. There are both environmental and
economic payoffs if terephthalic acid synthesis were to be practiced in water
commercially.
Background
Previous work in
our lab has demonstrated that high-temperature liquid water (HTW) at 300 �C is
a very promising medium. High
terephthalic acid yields (80 – 90%) and very high selectivities
(essentially 100%) are available. Though the technical feasibility of a HTW
process for terephthalic acid synthesis has been demonstrated, the reaction
must be improved and further refined if it is going to displace the current
acetic acid based process, which has benefited from years of continuous
refinement and optimization.
One barrier that
accompanies the HTW process at present is the low p-xylene concentrations
(about 0.02 mol/L) that have been used experimentally. Low p-xylene concentrations mean low
production of terephthalic acid per unit reactor volume. Thus, there is a need to explore
synthesis at higher concentrations of p-xylene to get greater
productivity. Work to date on this
project has focused on this objective of increasing productivity of
terephthalic acid synthesis in HTW by running at high p-xylene concentrations.
To work at
higher reactant concentrations, though, involves running the reaction as a
two-phase aqueous suspension since higher concentrations exceed the solubility
of p-xylene in HTW. It is not
known whether this two-phase processing scheme will be successful.
Results
We have conducted several sets of
stirred, batch oxidation experiments at 300 �C with p-xylene concentrations
higher than previously explored.
Experiments were done with p-xylene loadings ten times and 20 times
higher than those used in previous research. The reactor was initially loaded with p-xylene, water, and
catalysts. An important feature of
our experiments is that the oxygen gas was added to the pre-heated and pressurized
reactor contents. We tested both
incremental addition in small bursts and continuous oxygen addition. Table 1 summarizes the experimental
conditions and the results. The
product yields and selectivities in the table are those determined from analysis
of the material remaining in the reactor at the end of the run. The results show that high yields and
high selectivities (> 90%) to terephthalic acid are available only via
incremental addition of oxygen to the reactor system. Continuous addition of oxygen (runs 4 – 7) invariably
led to low yields and low selectivities.
Nevertheless, we have been successful in identifying synthesis
conditions that form high yields of terephthalic acid in HTW even at 10- and
20-fold higher p-xylene concentrations than used previously.
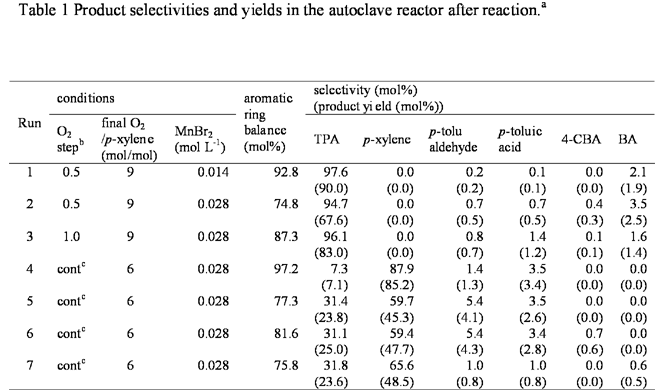
a Reaction condition; p-xylene 0.2 mol L-1.
b The molar ratio of O2 added to p-xylene initially loaded. The stoichiometric amount needed to convert p-xylene to TPA is 3.
c cont = continuous addition of O2
Back to top