Back to Table of Contents
44743-B10
Glow-Discharge Plasma as a Synthetic Medium for Nanocrystalline Non-Molecular Metal Oxides
Richard W. Schaeffer, Messiah College
Introduction
The plasma synthesis
project has continued to build on the progress from 2006-2007, which improved the
plasma chamber design, added a second plasma chamber, and added a mass-flow
controller system to better regulate gas delivery to the plasma.� During 2007-2008, we were able to synthesize
more than two dozen metal oxide films on glass and metal substrates.� These films were characterized for
stoichiometry using atomic absorption spectroscopy, phase composition using powder
x-ray diffraction, and morphology using optical and atomic force microscopy.� �
The
Plasma Reactor and Associated Systems
We continued modifying the
shape and orientation of the reactant cathode and substrate this year.� The hollow cathode design implimented last
year (using custom made glass sheaths to house the metal cathode) did not
resolve all of the problems associated with the plasma synthesis.� Although, as reported last year, the hollow
cathode design resulted in a more spatially directed plasma, a more concentrated
deposition of product on the substrate, and improved product deposition rates,
we are still struggling with poor reproduciblity.� We are successfully making metal and mixed
metal oxides, but product yields, stoichiometry, and morphology vary significantly
from sample to sample.� We attempted to
exercise better control over the system by directing the plasma gas flow
through the cathode to promote a more uniform product formation in the plasma
and a more evenly and completely deposited product on the substrate, however,
improvements were not consistently realized.�
We are currently working on another cathode design to address these
difficulties.�
The
enhancements to the plasma system made at the end of the last report period
have worked well.� The electronic mass
flow control of the plasma gases, argon and oxygen, have vastly improved the
control and stability of the plasma gas composition and flow.� �The MKS
type M100B mass-flow controllers and M10MB mass-flow meters allow excellent
stability and reproducibility in both gas pressure, flow, and mixing.� We are confident that the problems in product
formation (described above) are not derived from control over the plasma
gases.� Moreover, we have been successful
in stabilizing the second plasma chamber so that it now behaves very
consistently like the first plasma system with respect to gas control and
voltage-current realtionships.� Therefore
our continuing work will focus on redesigning the plasma cathode and substrate
to improve product yield, stoichiometry, and morphology.
Formation
and Characterization of Products
As mentioned
previously, we have made about two dozen different samples of metal oxides from
the� plasma system over this reporting
period.� As before, the products have
been analyzed for stoichiometry via atomic absorption spectroscopy, phase
composition via powder x-ray diffraction, and in several cases, morphology via optical
and atomic force microscopy. As reported in 2006-2007, products from the reaction
of a copper cathode in an oxygen plasma have shown a curiously wide ranging and
unusual elemental composition.� This
reporting period values ranged from Cu(1.05)O to Cu(1.22)O
in an argon rich plasma (3:1 moles Ar to O2) to Cu(2.31)
to Cu(3.27)O in an oxygen rich plasma (3:1 moles O2 to
Ar). �Again, the reproducibility of the
stoichiometry is not as good as desired, ranging between 10-30% rsd.� Like past work, part of the difficulty has
been the small yield of product ranging from less than 1.00 to 2.14 mg for
24-48 hour run times.� This increases the
relative uncertainty of stoichiometric determinations.� We are hopeful that continued work on the cathode
design will lead to higher and more reproducible yields and more consistent and
predictible product stoichiometry.�
We
have analyzed many of the plasma products with powder x-ray diffraction, which typically
reveal a crystalline phase of CuO (tenorite) with varying peak profiles and an
amorphous phase as illustrated in Figure 1 and Figure 2.� The variation in peak profile probably
represents differences in particle size and crystallinity. Finally, for many of
the� samples, atomic force microscopy revealed
an uneven �mountain range� product morphology on the surface of the substrate as
illustrated in Figure 3.� The height and diameter
of the individual �peaks� were about 50 and 400 nm, respectively.�
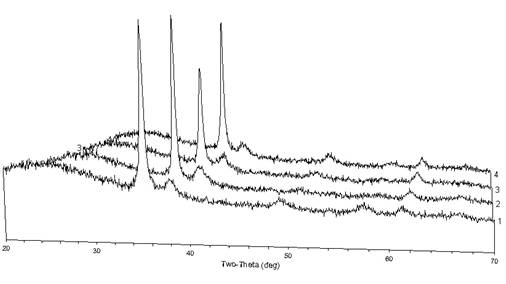
Figure �SEQ Figure \* ARABIC 1.�
Powder XRD patterns from four product films from a plasma synthesis
with a copper hollow cathode design.� The
peak 2θ positions are consistent with
CuO, but with apparently varying stoichiometry.
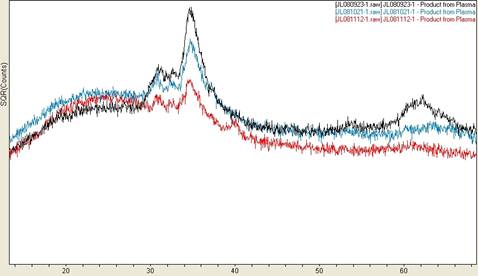
Figure 2.� Powder XRD patterns
from four product films from a plasma synthesis
with a copper hollow cathode design.� The
peak 2θ positions are consistent with
CuO, but with profiles that indicate smaller particle size or less
crystallinity.
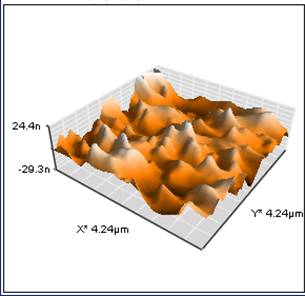
Figure �SEQ Figure \* ARABIC
3.� Three
dimensional AFM image of CuO
plasma product.
Back to top