Back to Table of Contents
42322-G5
Polypeptide Nano-Templating: A New Method for Creating Metal and Semiconductor Nanoscale Structures with 3D Shape Control
Stephen M. Kuebler, University of Central Florida
This project was designed to explore an approach to nano-materials called "Polypeptide Nano-Templating" (PPNT).� As envisioned PPNT could enable a wide range of materials to be fashioned into complex nano-scale three-dimensional (3D) forms by using discrete folded polypeptides as templates for directing the deposition of a second material onto a 3D nano-scale form.� The long-term goal was to develop a library of peptide sub-structures and deposition chemistries for creating materials having complex 3D nano-scale forms.
Our initial efforts focused on identifying chemistries that would be compatible with electroless deposition of metal onto rod-shaped peptide forms.� We soon found that very little is known about systematic means for controlling the nanoscale morphology of electrolessly deposited metal.� Additionally, all conditions we identified for electroless deposition of silver, copper, and gold yielded metal having a coarse nanoscale morphology for which the crystallite size was tens of nanometers or larger, and therefore unsuitable for conformal coverage of a sub-10-nm scale folded peptide.
We used surface functionalized polymer films as model systems for exploring the nanoscale morphology of electrolessly deposited metal.� We developed a process shown in Figure 1 for depositing silver onto cross-linked acrylate surfaces.� A polymer film was first treated with lithiated diaminopropane to bind amino-terminated groups to the surface covalently.� Next, the functionalized surface was treated with either (1) colloidal gold nanoparticles or (2) AuCl4-(aq).� Lastly, the functionalized film was treated with an aqueous solution of Ag+ and hydroquinone.� The pendant gold particles are needed to nucleate electroless growth of silver metal from the Ag+/hydroquinone solution.� We found that this process produced large silver nanoparticles, typically spherical in shape with diameter ranging from 50 - 150 nm.� A number of silver growth conditions were explored, and all were found to generate large nanocrystallites.
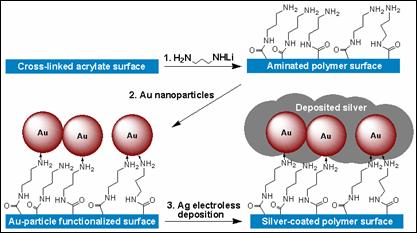
Figure 1.� Process developed to enable study of conditions that affect the nanoscale morphology of electrolessly deposited silver.
We explored the polymer/metallization process further as a means for generating metallized polymeric micro-structures.� In addition to PPNT, our group has a significant research effort focused on extending the range of material systems for fabricating 3D micro-structures using multi-photon direct laser writing (DLW).� We found that we could fabricate cross-linked acrylate micro-structures by DLW and then conformally coat the surfaces using the silvering process described above to generate conductive and optically reflective 3D micro-structures.� This has opened a new line of research for our group, as it enables an entirely new means for fabricating 3D metallodielectric micro-structures and studying their fundamental physical properties.� This research led to a publication in Advanced Functional Materials which featured our work on the cover (Fig. 2).� The work was co-authored by undergraduate David B. Torrance, chemistry graduate student Yun-Sheng Chen, and optics graduate student Amir Tal.
We have since extended the work by developing a process for creating metallized polymeric structures using the cross-linkable epoxide SU-8.� This work is significant because SU-8 is widely applied for fabricating functional micron-scale devices for micro-electromechanical systems (MEMS), micro-fluidics, and recently also photonics.� Our method for metallizing 3D SU-8 microstructures provides a new and flexible route to functional 3D devices using this high-performance polymer.� Figure 3 shows examples of metallized SU-8 �stack-of-logs� structures we created in our labs using this process.� This work was recently reported in Chemistry of Materials.� We have also extended these methods for deposition of copper onto SU-8 micro-scaffolds.
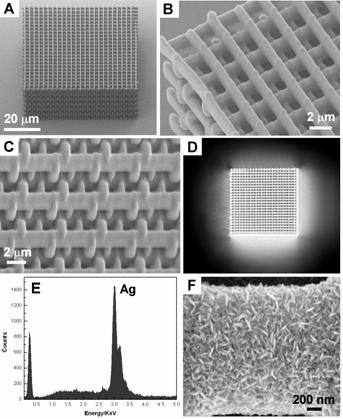
Figure 2.� Silvered polymeric �stack-of-logs� micro-structure supported on a glass coverslip substrate.� (A-C) SEM images of the metallized structure.� (D) Optical reflection microscopy image showing that the silvered structure is highly reflective.� (E) Energy dispersive X-ray spectrum of the structure.� The dominant peak at 3.0 keV proves that the structure is coated with Ag metal.� (F) High-magnification SEM image of the structure showing that Ag deposits as rice-shaped NPs when the silvering medium contains [Ag+] = 33 mM.
We found also that the nanoscale morphology of electrolessly deposited silver can be controlled through choice of reducing agent, silver ion concentration, inclusion of additives (such as gum Arabic), and the type of surface bound nucleating species that is used to seed electroless metal growth.� Figure 3 gives an example of how dramatically the nanoscale morphology can differ when two different types of nanoparticle (NP) nucleating seeds are used to catalyze deposition with all other processing conditions being kept the same.� These differences were found to be entirely reproducible.� Although the physical or chemical origins of this effect are not yet known to us, experiments involving detailed surface morphology analysis using transmission electron microscopy are planned.
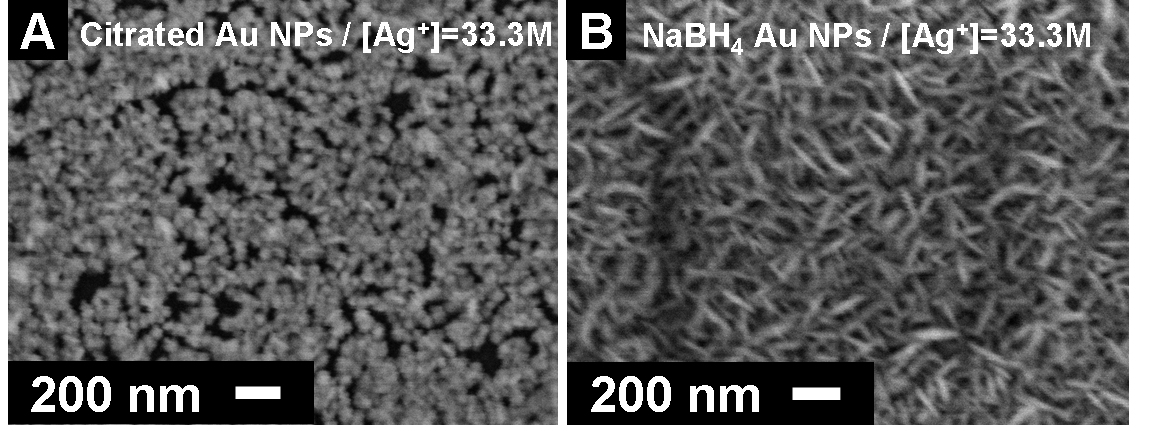
Figure 3. The SEM images of silver particles that were deposited on the different Au-NPs nucleated surfaces using a silver lactate/hydroquinone/gum Arabic bath. Image (A) shows spherical gain morphology of silver that was nucleated by surface bound citrated Au-NPs. Image (B) shows ellipsoidal grain morphology of silver that was nucleated by NaBH4-reduced Au-NPs.
Back to top