Introduction
The plasma synthesis project has realized significant progress this year in two broad areas: the design = of the plasma reaction system and the formation and characterization of produc= ts. First, we made refinements and add= itions to the plasma reactor and associated systems. These included improvements in the plasma chamber design, adding a second plasma chamber, and adding a mass-fl= ow controller system to better regulate gas delivery to the plasma. Secondly, we were able to synthesi= ze more than thirty metal oxide films on glass, metal, mica, and MgO substrates. These films were characterized for stoichiometry using atomic absorption spectroscopy, phase composition using a newly acquired powder x-ray diffractometer, and (in one case) morphology using a newly acquired atomic force microscope.
The Plasma Reactor and Associated Systems
One aspect of the plasma chamber design investigated this year was the shape and orientation of the reactant cathode. We moved to= a hollow cathode design using custom made glass sheaths to house the metal ca= thode. This resulted in a more spatially directed or focused plasma and a more concentrated deposition of product on= the substrate. Deposition rates improved by about a factor of five, although the results have suffered from= poor reproducibility (see below) and the studies need to be repeated. Another issue that remains is the = spatial homogeneity of the product across the substrate surface, which we are attem= pting to improve by directing the plasma gas flow through the cathode to promote a more uniform product formation in the plasma and a more evenly and complete= ly deposited product on the substrate. Ano= ther important enhancement of the plasma system was adding electronic mass flow control of the plasma gases, argon and oxygen, to improve the control and stability of the plasma gas composition and flow. Specifically, we obtained and inst= alled two MKS type M100B mass-flow controllers and a M10MB mass-flow meter. This upgrade to the system will al= low more accurate and stable control of the plasma gases and accurate mixing of argon and oxygen. As a result, we c= an exert much better control over the behavior of the plasma with respect to t= he synthesis of metal oxides. Th= e mass flow controllers were installed at the end of the summer research program, = so that much work remains to be done to characterize the system’s performance. Finally, we fini= shed setting up and running a second plasma chamber to increase productivity and assess reproducibility. The s= econd reactor is running and to date we have produced five copper oxide films from it. Our system is designed to= run both reactors simultaneously, which we have accomplished; however, plasma g= as pressure differences between the reactors have led to difficulties in establishing equivalent conditions in both reactors.
Formation and Characterization of Products
We have made about thirty different samples of metal oxides from plasma synthesis. The products have been analyzed for stoichiometry via atomic absorption spectroscopy, phase composition via pow= der x-ray diffraction, and morphology via atomic force microscopy. (The later two techniques have bec= ome available on site this year with a $125,000 grant from the Alden Trust fund= .) Products from the reaction of a co= pper cathode in an oxygen plasma have shown a curiously wide ranging and unusual composition from CuO0.86 to CuO4.6. However, the precision has been lo= w with relative stand deviations from about 10-50%. Moreover, we have seen a compositi= onal variation as a function of the distance between the cathode and substrate: = CuO3.02±0.79 at 0.80 cm and CuO1.95±0.26 at 1.30 cm. Unfortunately, the reproducibility= of these results has been poor in subsequent experiments. Part of the difficulty has been the small yield of product — from 0.55 to 2.88 mg, which increases the relative uncertainty of the stoichiometric determination. We are hopeful that the changes to= the hollow cathode design (see above) will lead to better and more reproducible yields. We have analyzed seve= ral products with powder x-ray diffraction, which revealed a crystalline phase = of CuO (tenorite) and an amorphous phase as illustrated in Figure 1. Finally, atomic force microscopy revealed a “carpet-like” morphology of product growing out from= the surface of the substrate as illustrated in Figures 2 and 3. The diameter of the individual “fibers” was about 200 nm.&nbs= p; We are in the process of trying to understand and control the factors that govern the exact morphology of the product.
<=!--[if gte vml 1]> 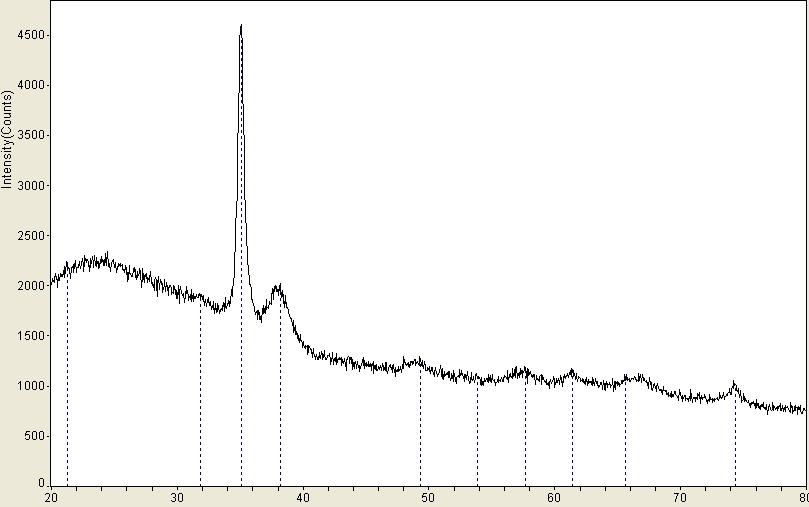
Figure SEQ Figur= e \* ARABIC 1. Powder XRD pattern from copper oxide product from plasma synthesis.
<=!--[if gte vml 1]> 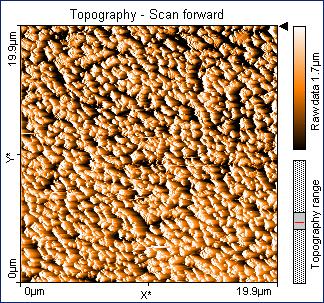
Figure SEQ Figur= e \* ARABIC 2. AFM image of CuO product from plasma.
<=!--[if gte vml 1]> 
Figure SEQ Figur= e \* ARABIC 3. Three dimensional AFM image of CuO plasma product.